Existen varias técnicas de mejora de la productividad que se pueden aplicar de manera efectiva en la organización. La mayoría de estas técnicas se desarrollaron en Japón después de la Segunda Guerra Mundial y, por lo tanto, tienen nombres japoneses. Estas técnicas aplicadas a todos los procesos internos, son muy utilizadas en el ámbito empresarial en la actualidad y las empresas que mejor las llevan adelante (en su mayoría automotrices japonesas) son aquellas que tienen menos niveles de accidentología laboral, rotación, ausentismo y mayores niveles de productividad y efeciencia.
Técnicas japonesas de mejora de la productividad
Jidoka – Es un concepto de Toyota destinado a describir la interfaz hombre-máquina de manera que las personas sigan siendo libres de ejercer juicio mientras que las máquinas cumplen su propósito. El sistema jidoka muestra fe en el trabajador como un pensador y le permite a todos los trabajadores el derecho de detener la línea en la que están trabajando. Jidoka a menudo se conoce como ‘automatización con una mente humana’. La forma de trabajar jidoka consta de tres principios, a saber (i) no hacer defectos, (ii) no transmitir defectos, y (iii) no aceptar defectos.
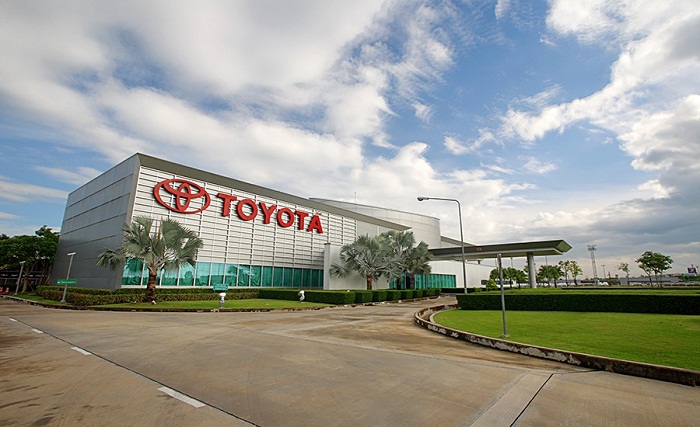
Heijunka – Se enfoca en lograr niveles consistentes de producción. Se define como ‘distribuir la producción de diferentes [tipos de cuerpo] de manera uniforme en el transcurso de un día’. Incorpora los principios del equilibrio de líneas al intentar equiparar las cargas de trabajo, nivelar la demanda mediante la creación de un inventory buffer (inventario utilizado para proteger al flujo de una operación o al programa de operaciones contra los efectos negativos causados por demoras en la entrega, problemas de calidad, entrega de la cantidad incorrecta, etc.) y la resposición de ese inventory buffer. Hay que proporcionar una carga de trabajo pareja para toda la fuerza de trabajo. Heijunka tiene la capacidad de reducir los tiempos de entrega al minimizar las pérdidas de tiempo debido a frecuentes cambios de proceso.
Kaizen – (Mejora continua) es un proceso impulsado por los empleados, en el que los empleados realizan una gran cantidad de esfuerzos de mejora continua.
Cinco Ss – Es un enfoque estructurado para lograr un lugar de trabajo limpio y ordenado mediante la fijación de lugar para todo. Five Ss es una abreviatura de las palabras japonesas (i) Seiri, (ii) Seiton, (iii) Seiso, (iv) Seiketsu y (v) Shitsuke. Seiri se está deshaciendo de los artículos innecesarios. Seiton consiste en organizar elementos (materiales, herramientas, indicadores) sistemáticamente para facilitar su recuperación. Seiso significa mantener el lugar de trabajo escrupulosamente limpio. Seiketsu está programando las operaciones regulares de limpieza y limpieza. Y Shitsuke está haciendo toda la tarea anterior para cumplir con los estándares acordados a intervalos acordados.
Eliminación de Muda: Muda significa desperdicio. La eliminación de Muda significa una reducción o eliminación continua y sistemática de los desechos. Hay siete tipos de desechos importantes. Estos son (i) sobreproducción de Muda, (ii) stock de Muda, (iii) transporte de Muda, (iv) defectos de Muda, (v) retraso de Muda, (vi) movimiento de Muda y (vii) sobre procesamiento de Muda. Ayuda a eliminar procesos redundantes o partes de procesos, eliminar actividades sin valor agregado, simplificar movimientos, minimizar la fatiga y reducir el tiempo de espera, etc.
Poka-Yoke: es un método de control y completo para la corrección de errores. Es un proceso de trabajo para eliminar errores inadvertidos para garantizar productos y servicios de calidad. Ayuda en la prevención de defectos y la detección de defectos.
SMED: el intercambio de un solo minuto de la matriz (SMED) es una técnica para realizar una operación de configuración en menor cantidad de tiempo. Afecta a una configuración de maquinaria para el cambio de uno a otro en un período de tiempo mínimo. Ayuda en la reducción del trabajo en curso, una mejor producción diaria promedio, una mayor capacidad y una entrega más rápida a los clientes.
Mantenimiento productivo total (TPM): TPM mantiene las máquinas en buenas condiciones de funcionamiento mediante el mantenimiento sistemático de los equipos para que fallen menos frecuentemente y el proceso de producción continúe sin interrupción.
Just-In-Time (JIT): ‘Justo a tiempo’ es una técnica de gestión que tiene como objetivo eliminar los residuos de todos los aspectos de la fabricación y sus actividades relacionadas. El término JIT se refiere a producir solo lo que se necesita, cuando se necesita y en la cantidad necesaria. El objetivo de JIT en la tienda de producción es reducir los plazos de entrega, minimizar el inventario, reducir la tasa de defectos a cero y lograrlos al costo mínimo. Hay tres ingredientes esenciales para la excelencia de producción efectiva a través de JIT. Estas son (i) técnicas de producción JIT cuyo objetivo es promover una respuesta rápida a la demanda de los clientes mientras se minimiza el inventario, (ii) una cultura de calidad total para buscar la excelencia tanto en el producto como en cada área de la actividad, incluido el servicio al cliente. compras, marketing, contabilidad, mantenimiento y diseño, etc., y (iii) participación de los empleados en el desarrollo de la organización a través de su cultura, su producción y otros procesos.
Kanban – Kanban es una técnica de programación de producción manual controlada por un proceso o por un operador de máquina. Kanban significa tarjeta en japonés, que se adjunta a una determinada cantidad de piezas o productos en la línea de producción que da instrucciones para la entrega de una determinada cantidad. La tarjeta Kanban después de que todas las piezas / productos han sido utilizados es devuelta por el operador a su origen. La producción se controla a través de la demanda proveniente de un cliente externo.
Gestión orientada a procesos (POM): la gestión tradicional se centra principalmente en los resultados y las personas en su logro final. La gerencia de Kaizen enfatiza el proceso para lograr los resultados. Los gerentes en POM son juzgados por las habilidades centradas en las personas como la gestión del tiempo, la educación y la capacitación, la participación entre equipos, la comunicación y el impulso moral.
Gestión visual: la gestión visual es el método para proporcionar, de forma claramente visible, tanto a la fuerza de trabajo como a la administración, información sobre el estado actual, incluido el objetivo de las diversas operaciones realizadas, así como varias piezas de trabajo encontradas en el lugar de trabajo.
Estándares de trabajo: los estándares de trabajo representan la mejor manera de hacer un trabajo y consisten en un conjunto de políticas, reglas, directivas y procedimientos documentados establecidos por la administración para todas las operaciones principales que permiten a los empleados realizar los trabajos sin errores y para permitir que la administración minimice variaciones en producción, calidad, trabajo en progreso y costo. Tres elementos del trabajo estandarizado son (i) tomar tiempo, (ii) secuencia de trabajo y (iii) trabajo en curso estándar. Los pasos clave para implementar los estándares de trabajo son (i) los temas clave en el proceso actual, (ii) mapear el proceso, (iii) mejorar el proceso, (iv) implementar el proceso y (v) mantener el proceso.
Ciclo PDCA / SDCA: el ciclo PDCA (Planificar, Hacer, Verificar, Actuar) es un ciclo de mejoras interminables que exige que los “planes” del equipo de trabajo (establecer un objetivo de mejora a través del plan de acción), “hacer” (implementar el plan) ” verifica (monitorea y evalúa los efectos, y ‘actúa’ (estandariza nuevos procedimientos o establece metas para una mejoría adicional). Como cada proceso es inicialmente inestable, se requiere estabilizarlo usando el ciclo SDCA (estandarizar-hacer-verificar-actuar). Por lo tanto, un ciclo de SDCA debe preceder a cada ciclo de PDCA para consolidar ganancias en el proceso actual antes de elevar el umbral estándar.
Control de proceso estadístico (SPC): el SPC es la aplicación de técnicas estadísticas para controlar un proceso y eliminar las variaciones del proceso debido a causas asignables. SPC necesita fuerza de trabajo para realizar muestreos periódicos de la calidad de la salida, ingresar datos en cuadros de control, analizar la tendencia y decidir cuándo cerrar el proceso y cuándo realizar ajustes / correcciones al proceso para evitar defectos.
Sistemas de sugerencias: los sistemas de sugerencias son fundamentales para la filosofía de Kaizen. Es el proceso propiedad de los empleados diseñado para beneficiar a la empresa, invitando a los empleados a sugerir / implementar cualquier idea, grande o pequeña, novedosa o mundana sobre cualquier aspecto de la vida de la organización.
METODOS MUY INTERESANTES PARA APLICAR EN NUETROS TRABAJOS.
GRACIAS POR ENSEÑARME